MENU
SG | SGD
SG | SGD
-
- Benchtop Centrifuges
- Floor-Standing Centrifuges
- Refrigerated Centrifuges
- Microcentrifuges
- Multipurpose Centrifuges
- High-Speed Centrifuges
- Accessories
- Ultracentrifuges
- Concentrator
- High-Speed and Ultracentrifugation Consumables
- Tubes
- Plates
- Device Management Software
- Sample and Information Management
No results found
Search Suggestions
Dissolved Oxygen Control in Bioreactors

Dissolved oxygen (DO) is a key driver affecting culture growth in bioreactors. However, cell lines and strains can have varied oxygen needs. The different types of oxygen requirements in bioreactors include:
- Aerobic culture. With a typical DO concentration of over 30%, aerobic conditions are required for mammalian cell cultures and many microbial cultures including E. coli.
- Microaerobic fermentation. With low concentrations of DO, microaerobic fermentation is often used for bacterial fermentation in the production of probiotics and the cultivation of some types of lactic acid bacteria.
- Anaerobic fermentation. Growing in the absence of oxygen, anaerobic microbes are commonly used to produce various chemicals including ethanol, lactic acid and acetic acid.
Read more
Read less
Webinar: DO control in bioreactors
Tailoring Oxygen Transfer: A Key Driver for Bioprocess Intensification - In this webinar you learn about strategies to tailor the dissolved oxygen concentration in the culture medium and to reproduce it at different scales.
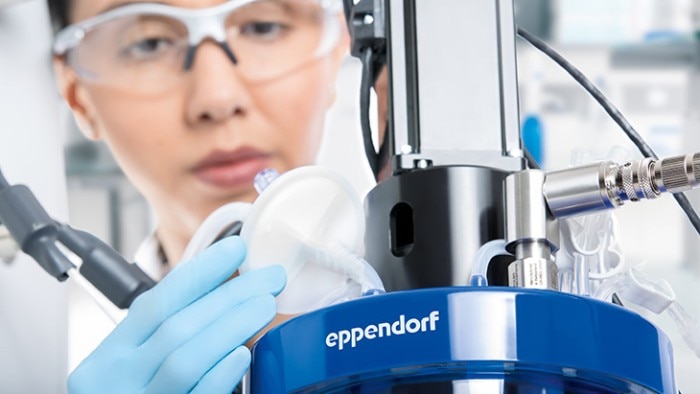
Principle of DO control in bioreactors
The maintenance of optimal oxygen levels is essential for culture growth and productivity. In aerobic cultures the growing cells consume oxygen and an effective bioreactor DO control system is therefore required to keep the dissolved oxygen concentration stable. Within these systems, DO sensors transmit readings to a bioreactor control software, which adjusts the DO concentration via adjusting the agitation via impellers, the influx of gases including air and oxygen using gas spargers, and/or gas composition. Contrastingly, the removal of oxygen from bioreactors can be achieved through sparging nitrogen or other anaerobic gasses.
Read more
Read less
When considering how to maximize the efficiency of DO control systems, several different parameters should be considered, including the choice of accessories, including DO sensor, sparger, and impeller and the choice of the control strategy. DO control strategies often involve cascades that define the activity of the different actuators for DO control. See below for advice on how each of these parameters should be optimized.
Read more
Read less
How to optimize DO control
What are DO cascades?
A DO cascade describes a specific sequence of actions that are employed to increase the DO concentration within bioreactors. As you move through the cascade, different actions of increasing intensity are initiated to ensure DO control is sufficient to optimize yield.
- Increased agitation - This is typically the first step of DO cascades and is achieved using an impeller, which is moved by a motor. The maximum agitation speed is not necessarily the theoretical maximum that can be achieved by the setup of choice. The user may decide to limit the maximum to a certain value, for example to avoid extensive shear stress to the cells.
- Air sparging - Once the maximum agitation speed has been reached, air sparging is increased in the system up to its maximum rate. Again, the maximum is user-defined.
- Oxygen enrichment - The air that is sparged into the system is gradually replaced by oxygen, until pure oxygen is sparged into the bioreactor.
Read more
Read less
What is a sparger? And how does the sparger type influence the DO?
Spargers are tools for introducing gasses into liquids through tiny pores. Different types of spargers exist with different functions in DO control, including macro-spargers and micro-spargers. Macro-spargers contain drilled holes that create larger gas bubbles. These are best suited for CO2 removal, as they are capable of capturing more gas into the bubbles that rise to the top. However, the large bubbles released by macro-spargers require agitation to release oxygen and so macro-spargers are unsuitable for more sensitive cultures such as mammalian cells. Even bigger gas bubbles are created by open pipe spargers. Contrastingly, micro-spargers have a much smaller pore diameter of a few micrometers wide. They therefore introduce smaller bubbles that are more effective at transferring oxygen while minimizing cell stress in bioreactors.
Read more
Read less
How does the type of gassing influence the DO?
In bioreactors, gasses introduced into the bioreactor can either be released into the headspace, or they can be released into the culture using spargers in a technique referred to as submerged gassing. Headspace gassing is often used to increase oxygen transfer into the culture, when agitation is too challenging or too detrimental to the cells. It is, however, less effective than submerged gassing. Submerged gassing is the most effective method of mass transfer of gasses in bioreactors. Spargers are typically located beneath the impeller to maximize the distribution of gas throughout the culture. However, sparging requires agitation for effective gas distribution, which can damage some types of cells.
Read more
Read less
What is an impeller? And how does the impeller type influence the DO?
Impellers - also known as agitators - are key components of bioreactors, providing agitation to increase oxygen transfer into the culture. A balance is needed to ensure that there is enough agitation for effective DO control, but not too much that it becomes damaging for more sensitive cell cultures, such as mammalian cells and stem cells. To achieve this, various impeller types are available that are suited towards different types of cultures and DO requirements. Blade orientation largely impacts the agitation of the impeller, with axial blades providing more gentle mixing than radial. Impellers suitable for more sensitive cell cultures include marine impellers, which have axial blades with convex back sides to provide gentle mixing. Another example is the pitched-blade impeller, which has blades oriented at a certain angle (often a 45° angle is used) to provide effective, yet gentle mixing for viscous or sensitive cell cultures. Impellers suitable for more robust cultures includes Rushton impellers, with flat, radial blades. Rushton impellers are commonly used for microbial fermentation in bioreactors. However, other factors related to the impeller design can influence the DO transfer rate, including the number of blades, the impeller speed and diameter.
Read more
Read less
What is 100 % DO? And how is this different to the total oxygen concentration?
The % DO is a measure of how much oxygen is dissolved in a solution. This is different to the total oxygen concentration, as DO depends on the solubility of oxygen in a solution. For example, 100 % DO in one solution could have a different total oxygen concentration than another solution with 100 % DO. Solubility can be impacted by several environmental factors such as the temperature and the pressure. Therefore, DO sensor recalibration is always required under different process conditions.
Read more
Read less
What kind of DO sensors exist and how are they calibrated?
Polarographic and optical DO sensors
There are two main types of DO sensors, polarographic and optical. Polarographic DO sensors measure the electrical current within the solution to infer the oxygen concentration. Optical DO sensors measure the luminescence of a solution using blue light, with the presence of dissolved oxygen decreasing the luminescence. Find out more about the measurement principle of these sensor types and get guidance how to calibrate them:
Read more
Read less
KLa and OTR
What are kLa and OTR? And how are these parameters important for DO control?
kLA and OTR measure the efficiency of DO transfer into the bioreactor culture, hence are important parameters for DO control. The kLA is the volumetric mass transfer coefficient. This describes the rate of oxygen or gas transfer into the culture, per unit of volume, per hour. kLA is strongly associated with features of bioreactor design, influenced by bubble size, agitation speed, impeller type and sparger type. OTR is the Oxygen Transfer Rate. It is equal the kLA multiplied by the O2 concentration gradient and therefore proportional to the kLA.Therefore, kLA and OTR values are paramount to the design of DO control systems. These are important values to consider when implementing new bioreactor equipment or when changing the operating conditions. When scaling-up for example, it is important to choose differently sized bioreactors with similar oxygen transfer capabilities to be able to reproduce the conditions optimized at small scale at larger scales.
Read more
Read less
Bioreactor control systems for effective DO control
The Eppendorf bioreactor control systems and software provide smart solutions for DO control. They
- Are compatible with analog DO sensors and, dependent on the control system, digital Mettler Toledo ISM® or Hamilton ARC® DO sensors
- Are compatible with polarographic and optical DO sensors
- Enable the set-up of customizable DO cascades, with precise agitation and gas sparging to provide automated DO control
- The Auto Calibrate software feature of the BioFlo® 320 and BioFlo® 720 bioreactor control systems automatically polarizes and calibrates DO sensors by the user’s preferred calibration methodology. This helps reducing variations between runs and contributes to bioprocess reproducibility.
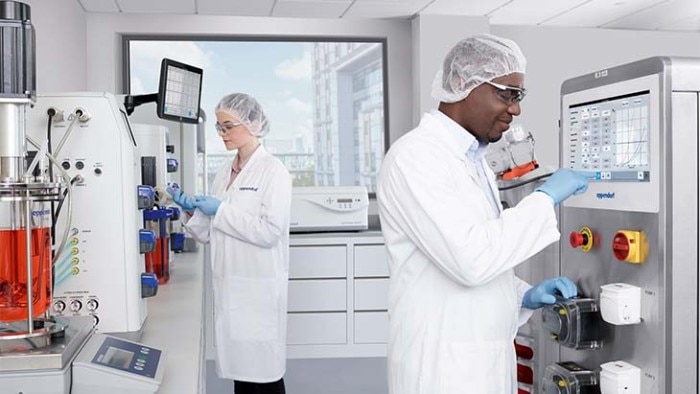